Effektive Prozessoptimierung durch Lean Management und SMED-Technik
Einführung in Lean Management
Definition von Lean Management
Lean Management ist eine Managementphilosophie, die darauf abzielt, die Effizienz und Effektivität von Unternehmensprozessen zu maximieren, indem Verschwendung reduziert und kontinuierliche Verbesserungen vorangetrieben werden. Das Konzept des Lean Managements stammt ursprünglich aus der Automobilindustrie, speziell von Toyota, und hat sich seitdem auf verschiedene Branchen und Unternehmensbereiche ausgeweitet. Im Mittelpunkt von Lean Management stehen die Schaffung von Mehrwert für den Kunden sowie die Optimierung von Prozessen durch die Beseitigung von Verschwendung in Form von unnötigen Ressourcen, Zeit oder Kosten. Durch die Anwendung von Lean-Prinzipien streben Unternehmen danach, schlanke Prozesse zu etablieren, die eine hohe Qualität, Flexibilität und Effizienz gewährleisten.
Ziele und Prinzipien von Lean
Die Ziele des Lean Managements umfassen in erster Linie die Maximierung des Kundennutzens durch die Eliminierung von Verschwendung in sämtlichen Unternehmensprozessen. Dabei stehen Effizienzsteigerung, Qualitätsverbesserung, Kostensenkung und die Reduzierung von Durchlaufzeiten im Fokus. Durch die Anwendung von Lean sollen Prozesse schlanker gestaltet, Engpässe identifiziert und behoben sowie die Mitarbeiter in kontinuierlichen Verbesserungsprozessen aktiv eingebunden werden. Prinzipien von Lean beinhalten unter anderem die Wertschöpfung aus Kundensicht, die Schaffung von transparenten Prozessen, die Minimierung von Beständen, die kontinuierliche Verbesserung der Abläufe sowie die Schaffung einer Kultur des Respekts und der Teamarbeit. Durch die konsequente Umsetzung dieser Prinzipien strebt Lean Management eine schlanke, effiziente und flexible Produktion an, die sich durch hohe Qualität, Flexibilität und Reaktionsfähigkeit auszeichnet.
SMED-Technik im Lean Management
Bedeutung von SMED (Single-Minute Exchange of Die)
Die SMED-Technik im Lean Management spielt eine entscheidende Rolle bei der Optimierung von Prozessen in Unternehmen. SMED steht für „Single-Minute Exchange of Die“ und zielt darauf ab, Rüstzeiten drastisch zu reduzieren. Durch die Anwendung der SMED-Methode können Unternehmen ihre Effizienz steigern und somit wertvolle Zeit und Ressourcen einsparen. Die Reduzierung der Rüstzeiten ermöglicht es, flexibler auf Kundenbedürfnisse zu reagieren und die Produktivität zu erhöhen. Daher ist die Bedeutung von SMED im Lean Management nicht zu unterschätzen und bietet Unternehmen die Möglichkeit, ihre Wettbewerbsfähigkeit zu stärken.
Ursprung und Entwicklung der SMED-Methode
Die SMED-Methode, auch bekannt als „Single-Minute Exchange of Die“, wurde von Shigeo Shingo entwickelt, einem japanischen Ingenieur und Berater, der eng mit Toyota zusammenarbeitete. Der Ursprung der SMED-Technik liegt in den Bemühungen von Toyota, ihre Produktionsprozesse zu optimieren und die Effizienz zu steigern. Shingo stellte fest, dass ein Großteil der Stillstandzeiten in der Produktion auf Rüstzeiten zurückzuführen war, die bei einem Werkzeugwechsel anfielen.
In den 1950er Jahren entwickelte Shingo die SMED-Methode, um diese Rüstzeiten drastisch zu reduzieren. Der Name „Single-Minute Exchange of Die“ bezieht sich darauf, dass das Ziel darin besteht, den Werkzeugwechsel in den Bereich von Minuten, idealerweise unter einer Minute, zu bringen. Shingo unterschied zwischen internen und externen Vorgängen während des Rüstprozesses und konzentrierte sich darauf, die internen Vorgänge zu minimieren oder sogar zu eliminieren.
Durch die Einführung der SMED-Technik konnten Unternehmen die Rüstzeiten erheblich verkürzen, was zu einer Steigerung der Produktivität, Flexibilität und Effizienz führte. Die SMED-Methode wurde schnell zu einem zentralen Bestandteil des Lean Managements und wird heute in verschiedenen Branchen weltweit erfolgreich eingesetzt.
Die Schritte der SMED-Methode
Identifizierung von internen und externen Vorgängen
Bei der SMED-Methode (Single-Minute Exchange of Die) ist es entscheidend, zunächst die internen und externen Vorgänge während des Rüstvorgangs zu identifizieren. Interne Vorgänge sind dabei Schritte, die ausschließlich während des Stillstands der Maschine ausgeführt werden können, während externe Vorgänge auch während des laufenden Betriebs durchgeführt werden können. Diese Unterscheidung ermöglicht es, gezielt die internen Vorgänge zu minimieren und zu optimieren, um so die Rüstzeit insgesamt zu reduzieren. Durch die klare Zuordnung von internen und externen Vorgängen wird eine systematische Herangehensweise an die Optimierung des Rüstprozesses ermöglicht.
Trennung von internen und externen Vorgängen
Bei der SMED-Methode (Single-Minute Exchange of Die) ist es entscheidend, zwischen internen und externen Vorgängen zu unterscheiden. Interne Vorgänge sind dabei alle Aktivitäten, die nur während des Stillstands der Maschine durchgeführt werden können, während externe Vorgänge auch während des Betriebs vorbereitet werden können. Durch die Trennung dieser beiden Arten von Vorgängen wird angestrebt, die Rüstzeiten signifikant zu reduzieren. Dieser Schritt ermöglicht es, die Effizienz des Umrüstprozesses zu steigern, da externe Vorgänge parallel zu den internen durchgeführt werden können. Somit wird die Stillstandszeit der Maschine minimiert und die Produktivität erhöht.
Umwandlung interner in externe Vorgänge
Nachdem die internen und externen Vorgänge identifiziert und voneinander getrennt wurden, folgt in der SMED-Methode der Schritt der Umwandlung interner in externe Vorgänge. Dies bedeutet, dass alle möglichen Schritte des Rüstvorgangs so gestaltet werden, dass sie extern und somit parallel zum laufenden Prozess durchgeführt werden können. Dadurch wird die Zeit, die für den Werkzeugwechsel benötigt wird, deutlich reduziert.
Die Umwandlung interner in externe Vorgänge erfordert eine genaue Analyse und Neugestaltung der Abläufe. Es werden beispielsweise Hilfsmittel oder spezielle Vorrichtungen eingesetzt, um bestimmte Schritte außerhalb der eigentlichen Maschine durchführen zu können. Dies ermöglicht es, den Werkzeugwechsel effizienter zu gestalten und die Stillstandszeiten zu minimieren.
Durch die Umwandlung interner in externe Vorgänge können Unternehmen die Rüstzeiten weiter optimieren und die Produktionsabläufe deutlich beschleunigen. Dies trägt maßgeblich zur Steigerung der Effizienz und Flexibilität bei, was letztendlich zu einer Verbesserung der Wettbewerbsfähigkeit führt.
Optimierung der externen Vorgänge
Nachdem die internen Vorgänge optimiert und vereinfacht wurden, konzentriert sich die SMED-Methode auf die Optimierung der externen Vorgänge. Externe Vorgänge sind diejenigen, die während des Rüstvorgangs nicht verändert werden können, da sie zeitlich unabhängig von der eigentlichen Rüstung sind. Das Ziel der Optimierung externer Vorgänge besteht darin, ihre Dauer zu minimieren, um die Gesamtrüstzeit weiter zu reduzieren.
Um die externen Vorgänge zu optimieren, werden verschiedene Maßnahmen ergriffen. Dazu gehören beispielsweise die Vorbereitung von Werkzeugen und Materialien im Voraus, die Bereitstellung von Unterstützungssystemen für den Rüstprozess sowie die Schulung der Mitarbeiter, um effizienter zu arbeiten. Durch die gezielte Optimierung externer Vorgänge können Engpässe beseitigt und die Effizienz des gesamten Rüstprozesses verbessert werden.
Standardisierung des Prozesses
Die Standardisierung des Prozesses ist ein entscheidender Schritt in der SMED-Methode, um die Effizienz und Wirksamkeit der Rüstzeitoptimierung sicherzustellen. Durch die Entwicklung und Implementierung von standardisierten Abläufen werden wiederholbare und konsistente Ergebnisse erzielt. Dies ermöglicht es, Rüstzeiten weiter zu reduzieren und die Effizienz des gesamten Umrüstprozesses zu maximieren.
Die Standardisierung umfasst die Dokumentation aller optimierten Schritte und Verfahren, die während der Anwendung der SMED-Technik identifiziert wurden. Dies beinhaltet klare Anweisungen, Checklisten, Arbeitsanweisungen und eventuelle Schulungen für die Mitarbeiter, um sicherzustellen, dass die neuen Prozesse effektiv umgesetzt werden können.
Durch die Standardisierung des Prozesses wird auch sichergestellt, dass das erlangte Wissen und die Optimierungen langfristig im Unternehmen verankert sind. Es erleichtert die kontinuierliche Überwachung, Messung und Verbesserung der Rüstzeiten, da ein einheitlicher Rahmen geschaffen wurde, an dem sich alle Beteiligten orientieren können.
Insgesamt trägt die Standardisierung des Prozesses dazu bei, die Nachhaltigkeit der Rüstzeitoptimierung durch die SMED-Methode zu gewährleisten und den langfristigen Erfolg in Bezug auf Effizienzsteigerung und Produktivitätssteigerung zu unterstützen.
Anwendung von SMED in verschiedenen Branchen
Beispiele für die Anwendung von SMED in der Automobilbranche
In der Automobilbranche wird die SMED-Methode häufig eingesetzt, um schnelle und effiziente Produktionswechsel zu ermöglichen. Ein Beispiel für die Anwendung von SMED in der Automobilbranche ist die Reduzierung der Rüstzeiten bei der Montage von Fahrzeugen. Durch die Implementierung der SMED-Technik konnten Automobilhersteller die Zeit für den Wechsel zwischen verschiedenen Produktionsläufen erheblich verkürzen. Dies führte zu einer erhöhten Flexibilität in der Produktion und ermöglichte es den Unternehmen, auf Kundenanforderungen schneller zu reagieren. Die Anwendung von SMED hat somit dazu beigetragen, die Effizienz und Wettbewerbsfähigkeit in der Automobilbranche zu steigern.
Anwendung von SMED in der Lebensmittelindustrie
In der Lebensmittelindustrie hat sich die Anwendung der SMED-Methode als äußerst effektiv erwiesen, um die Effizienz der Produktionsprozesse zu steigern. Ein wichtiger Aspekt in der Lebensmittelproduktion ist die schnelle Umstellung der Produktionslinien, um auf verschiedene Produkte oder Chargen reagieren zu können. Durch die Implementierung von SMED können Rüstzeiten erheblich reduziert werden, was zu einer erhöhten Flexibilität und Effizienz führt.
Ein Beispiel für die Anwendung von SMED in der Lebensmittelindustrie ist die Verarbeitung von Milchprodukten. Durch die Optimierung der Rüstzeiten bei der Umstellung der Abfüllanlagen für verschiedene Milchprodukte können Hersteller ihre Produktionskapazitäten besser auslasten und schneller auf Marktnachfragen reagieren. Dies führt nicht nur zu Kosteneinsparungen, sondern auch zu einer verbesserten Lieferfähigkeit und Produktqualität.
Darüber hinaus ermöglicht die Anwendung von SMED in der Lebensmittelindustrie eine bessere Kontrolle über den gesamten Produktionsprozess, was wiederum zu einer Steigerung der Produktivität und Rentabilität führt. Indem unnötige Wartezeiten und Stillstandszeiten reduziert werden, können Lebensmittelhersteller ihre Produktionsziele effektiver erreichen und gleichzeitig die Kundenzufriedenheit steigern.
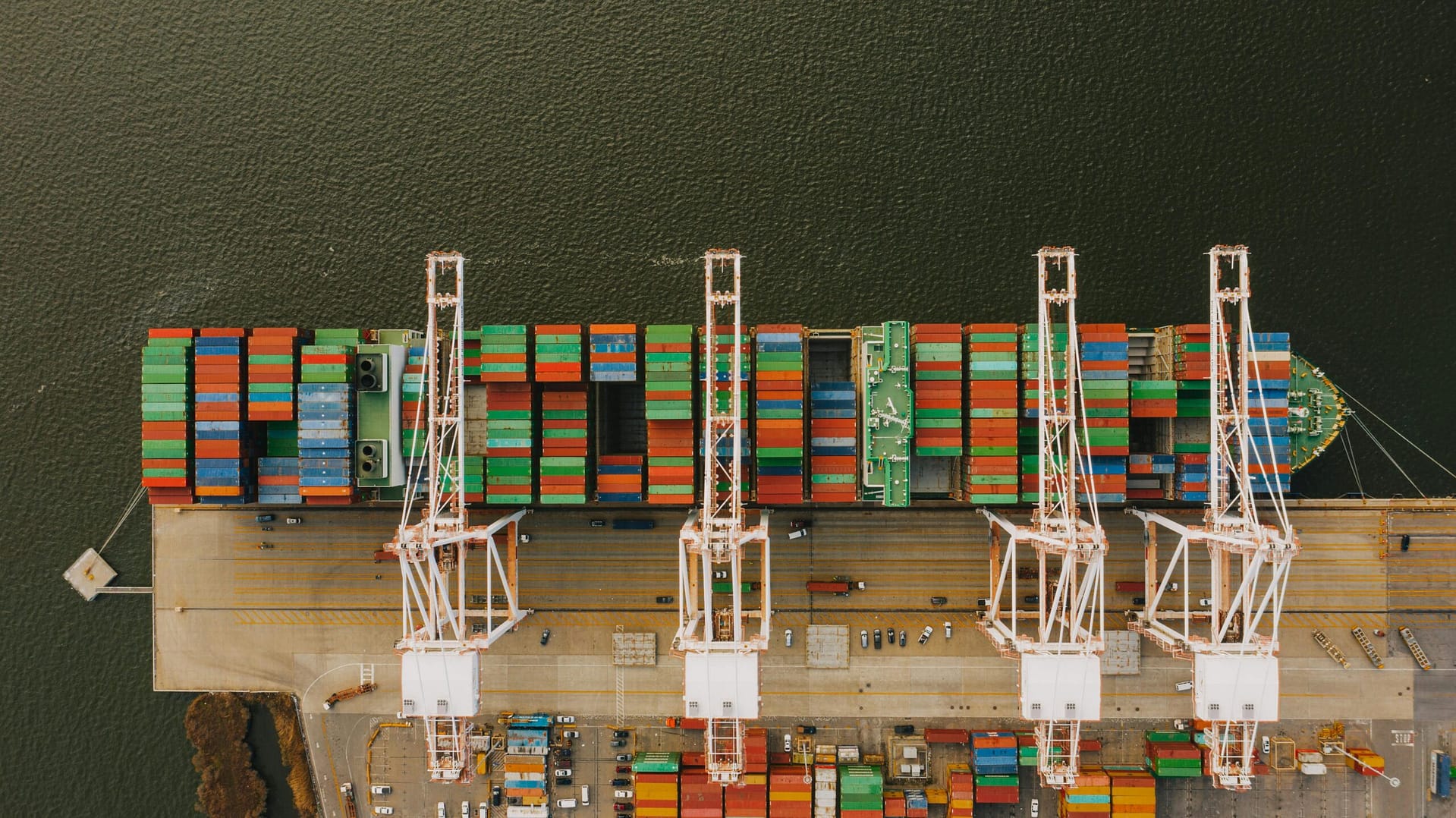
Vorteile der SMED-Methode
Reduzierung von Rüstzeiten
Die SMED-Methode bietet eine Vielzahl von Vorteilen für Unternehmen, darunter die signifikante Reduzierung von Rüstzeiten. Durch die Anwendung der Schritte der SMED-Methode können Rüstzeiten drastisch verkürzt werden, was zu einer Steigerung der Effizienz und Produktivität führt. Statt Stunden für den Wechsel von Werkzeugen oder Maschineneinstellungen zu benötigen, können diese Prozesse mit SMED auf Minuten reduziert werden. Diese Zeitersparnis ermöglicht es Unternehmen, flexibler auf Kundenanforderungen zu reagieren und die Auslastung ihrer Anlagen zu maximieren. Letztendlich trägt die Reduzierung von Rüstzeiten dazu bei, die Gesamtkosten zu senken und die Wettbewerbsfähigkeit des Unternehmens zu stärken.
Steigerung der Flexibilität und Effizienz
Die Anwendung der SMED-Methode führt zu einer signifikanten Steigerung der Flexibilität und Effizienz in Produktionsprozessen. Durch die Reduzierung der Rüstzeiten können Unternehmen schneller auf Marktanforderungen reagieren und flexibler auf Kundenwünsche eingehen. Die Effizienz wird gesteigert, da weniger Zeit für den Wechsel zwischen verschiedenen Produktionsaufträgen benötigt wird, was zu einer verbesserten Auslastung der Produktionsanlagen führt. Darüber hinaus ermöglicht die SMED-Methode eine bessere Nutzung der verfügbaren Ressourcen und eine insgesamt effizientere Produktion, was letztendlich zu Kosteneinsparungen und einer Steigerung der Wettbewerbsfähigkeit des Unternehmens führt.
Kosteneinsparungen und Qualitätsverbesserung
Die SMED-Methode, Single-Minute Exchange of Die, bietet nicht nur die Möglichkeit, Rüstzeiten zu reduzieren und die Flexibilität zu steigern, sondern führt auch zu signifikanten Kosteneinsparungen und Qualitätsverbesserungen in Unternehmen. Durch die schnelle Umstellung von Produktionsanlagen können Unternehmen ihre Produktionskapazitäten besser ausnutzen und die Gesamtkosten senken. Darüber hinaus ermöglicht die Reduzierung von Umrüstzeiten eine effizientere Nutzung von Maschinen und Arbeitskräften, was zu einer Optimierung der Kostenstruktur führt.
Ein weiterer wichtiger Aspekt sind die Qualitätsverbesserungen, die durch die Anwendung der SMED-Methode erzielt werden können. Durch kürzere Rüstzeiten und eine standardisierte Vorgehensweise wird das Risiko von Fehlern und Ausschuss reduziert. Dies trägt dazu bei, die Produktqualität zu steigern und die Kundenzufriedenheit zu erhöhen. Zudem ermöglicht die schnellere Umstellung auf neue Aufträge eine flexiblere Produktion, die es Unternehmen erleichtert, auf sich ändernde Marktanforderungen und Kundenwünsche zu reagieren.
Herausforderungen bei der Implementierung von SMED
Widerstand gegen Veränderungen
Widerstand gegen Veränderungen ist eine der Hauptprobleme bei der Implementierung von SMED in Unternehmen. Mitarbeiter sind oft skeptisch gegenüber neuen Methoden und Prozessen, insbesondere wenn sie ihre gewohnten Arbeitsweisen ändern sollen. Dies kann zu Widerstand auf verschiedenen Ebenen führen, sei es auf individueller Ebene bei den Mitarbeitern oder auf organisatorischer Ebene durch Führungskräfte.
Es ist wichtig, diesen Widerstand ernst zu nehmen und gezielt zu adressieren. Kommunikation spielt hier eine entscheidende Rolle, um die Mitarbeiter über die Vorteile von SMED zu informieren und sie aktiv in den Veränderungsprozess einzubeziehen. Schulungen und Workshops können dazu beitragen, das Verständnis für die SMED-Methode zu vertiefen und Ängste abzubauen.
Ein weiterer Aspekt des Widerstands gegen Veränderungen ist die Angst vor dem Unbekannten. Mitarbeiter können unsicher sein, wie sich die Einführung von SMED auf ihre tägliche Arbeit auswirken wird und ob sie mit den neuen Anforderungen Schritt halten können. Hier ist es wichtig, Unterstützung und Coaching anzubieten, um den Mitarbeitern Sicherheit zu geben und sie auf dem Weg zur Umsetzung von SMED zu begleiten.
Schulungsbedarf für Mitarbeiter
Ein wesentlicher Aspekt bei der Implementierung der SMED-Methode sind die Schulungsbedürfnisse der Mitarbeiter. Da SMED darauf abzielt, die Effizienz und Flexibilität in den Produktionsprozessen zu steigern, ist es entscheidend, dass alle beteiligten Mitarbeiter das Konzept und die Schritte der Methode vollständig verstehen. Dies erfordert in vielen Fällen spezielle Schulungen und Trainings, um sicherzustellen, dass das gesamte Team in der Lage ist, die SMED-Prinzipien erfolgreich umzusetzen.
Die Schulungen sollten nicht nur theoretisches Wissen vermitteln, sondern auch praktische Übungen beinhalten, um den Mitarbeitern zu ermöglichen, das Gelernte direkt in ihren Arbeitsabläufen anzuwenden. Es ist wichtig, dass die Mitarbeiter die Bedeutung der Reduzierung von Rüstzeiten verstehen und motiviert sind, aktiv an der Umsetzung von SMED mitzuwirken.
Darüber hinaus müssen Führungskräfte und Manager sicherstellen, dass die Mitarbeiter kontinuierlich unterstützt und begleitet werden, während sie die SMED-Methode in ihren täglichen Aufgaben integrieren. Regelmäßige Feedback-Schleifen und Überprüfungen sind entscheidend, um sicherzustellen, dass die Implementierung von SMED erfolgreich ist und langfristig positive Auswirkungen auf die Produktionsprozesse hat.
Kontinuierliche Überwachung und Verbesserung
Die kontinuierliche Überwachung und Verbesserung sind wesentliche Herausforderungen bei der Implementierung der SMED-Methode im Lean Management. Nachdem die Schritte der SMED-Methode erfolgreich umgesetzt wurden, ist es entscheidend, den Prozess regelmäßig zu überwachen, um sicherzustellen, dass die Rüstzeiten weiterhin minimiert werden und die Effizienz gesteigert wird.
Dazu ist es erforderlich, klare Leistungsindikatoren festzulegen, um den Erfolg der Implementierung zu messen. Regelmäßige Audits und Reviews des Prozesses helfen dabei, potenzielle Engpässe oder Probleme frühzeitig zu identifizieren und Maßnahmen zur kontinuierlichen Verbesserung einzuleiten.
Ein weiterer Aspekt ist die Einbindung der Mitarbeiter in den Überwachungs- und Verbesserungsprozess. Schulungen und Trainings sind notwendig, um sicherzustellen, dass das Team die Bedeutung der SMED-Methode versteht und aktiv an der Umsetzung und Optimierung des Prozesses teilnimmt. Nur durch eine kontinuierliche Überwachung und Verbesserung kann langfristig sichergestellt werden, dass die Vorteile der SMED-Methode nachhaltig in der Organisation verankert werden.
Fazit
Zusammenfassung der wichtigsten Erkenntnisse zu SMED
Zusammenfassend lässt sich sagen, dass die SMED-Methode im Lean Management eine entscheidende Rolle bei der Reduzierung von Rüstzeiten spielt. Durch die klare Strukturierung des Rüstprozesses und die Identifizierung sowie Optimierung interner und externer Vorgänge ermöglicht SMED eine Steigerung der Effizienz und Flexibilität in Produktionsprozessen. Die Anwendung von SMED führt nicht nur zu Kosteneinsparungen, sondern auch zu einer Verbesserung der Produktqualität. Es ist jedoch wichtig zu beachten, dass die Implementierung von SMED auf verschiedene Herausforderungen stoßen kann, wie beispielsweise Widerstände gegen Veränderungen und den Schulungsbedarf für Mitarbeiter. Dennoch bietet die SMED-Methode Unternehmen die Möglichkeit, ihre Prozesse kontinuierlich zu optimieren und somit langfristig wettbewerbsfähig zu bleiben.
Bedeutung von SMED für die Effizienzsteigerung in Unternehmen
Die SMED-Methode spielt eine entscheidende Rolle bei der Effizienzsteigerung in Unternehmen. Durch die Reduzierung von Rüstzeiten ermöglicht SMED eine höhere Flexibilität in der Produktion, da Umrüstungszeiten minimiert werden und Produktionsanlagen schneller auf neue Aufträge umgestellt werden können. Dies führt zu einer Steigerung der Gesamteffizienz, da Stillstandszeiten reduziert und die Produktionskapazität besser ausgelastet werden können. Darüber hinaus ermöglicht SMED Kosteneinsparungen, da weniger Zeit und Ressourcen für Umrüstungen benötigt werden. Die Qualitätsverbesserung ist ebenfalls ein wichtiger Aspekt, da stabilere Prozesse zu weniger Fehlern und somit zu einer höheren Produktqualität führen. Insgesamt ist die Anwendung von SMED ein wesentlicher Schritt für Unternehmen auf dem Weg zu schlankeren und effizienteren Betriebsabläufen.